Understanding NOx and SOx Regulations:
A Guide for Combustion Operators
As emissions regulations become more stringent worldwide, the need to control pollutants like NOx (nitrogen oxides) and SOx (sulphur oxides) has never been greater. These emissions are major contributors to air pollution and environmental damage, and industries operating combustion systems must take proactive steps to meet regulatory standards. In this guide, we will explore the key solutions for maintaining compliance while optimising performance.
Understanding the environmental and health impacts of NOx and SOx emissions is critical. NOx contributes to smog formation and can lead to respiratory issues, while SOx emissions lead to acid rain and environmental acidification. Governments and regulatory bodies worldwide are tightening limits to protect public health and ecosystems, making compliance essential for industrial operators.
Exposure to high levels of NOx and SOx can have severe consequences for both human health and the environment. NOx emissions contribute to ground-level ozone formation, which can lead to respiratory illnesses such as asthma and bronchitis. Additionally, NOx reacts with water, oxygen, and other chemicals to create acid rain, which damages crops, forests, and aquatic ecosystems.
Similarly, SOx emissions are also a major cause of acid rain and can result in soil degradation, harm to marine life, and infrastructure corrosion. These negative effects highlight the urgent need for industries to adopt cleaner combustion technologies.
This article will provide an overview of the different ways in which industries are adapting to new regulations and Emission Limit Values (ELV). If you would like to know more about lowering the emissions of your plant, contact us today at webenquiry@saacke.co.uk and a member of the team will be in touch to discuss.
The Importance of Low-NOx Burners in Maintaining Compliance
Reducing emissions at the source is the most effective way to tackle NOx and SOx. Modern combustion systems equipped with low-NOx burners, like the SAACKE TEMINOX pressure jet for instance, will minimise NOx pollutants during combustion by optimising fuel-air mixing and reducing peak flame temperatures.
The use of low-sulphur fuels is a responsible and effective way to reduce SOx emissions from the get-go. Switching to alternative fuels, such as biofuels or hydrogen blends, can further support emissions reduction while maintaining efficiency. Many industries are now exploring fuel flexibility to future-proof their operations against evolving regulations and fuel availability.
At SAACKE, our range of advanced low-NOx burners and combustion solutions are specifically designed to meet the strictest global emissions limits, one such example being the Medium Combustion Plant Directive (MCPD) which came into law in 2018 and this year became a strict deadline for existing Medium Combustion Plant between 5MW-50MW.
By delivering precise combustion control, we help industries not only comply with regulations but also improve fuel efficiency and reduce energy costs. For operators, this means achieving cleaner combustion without compromising on reliability or performance – a critical step in sustainable operations.
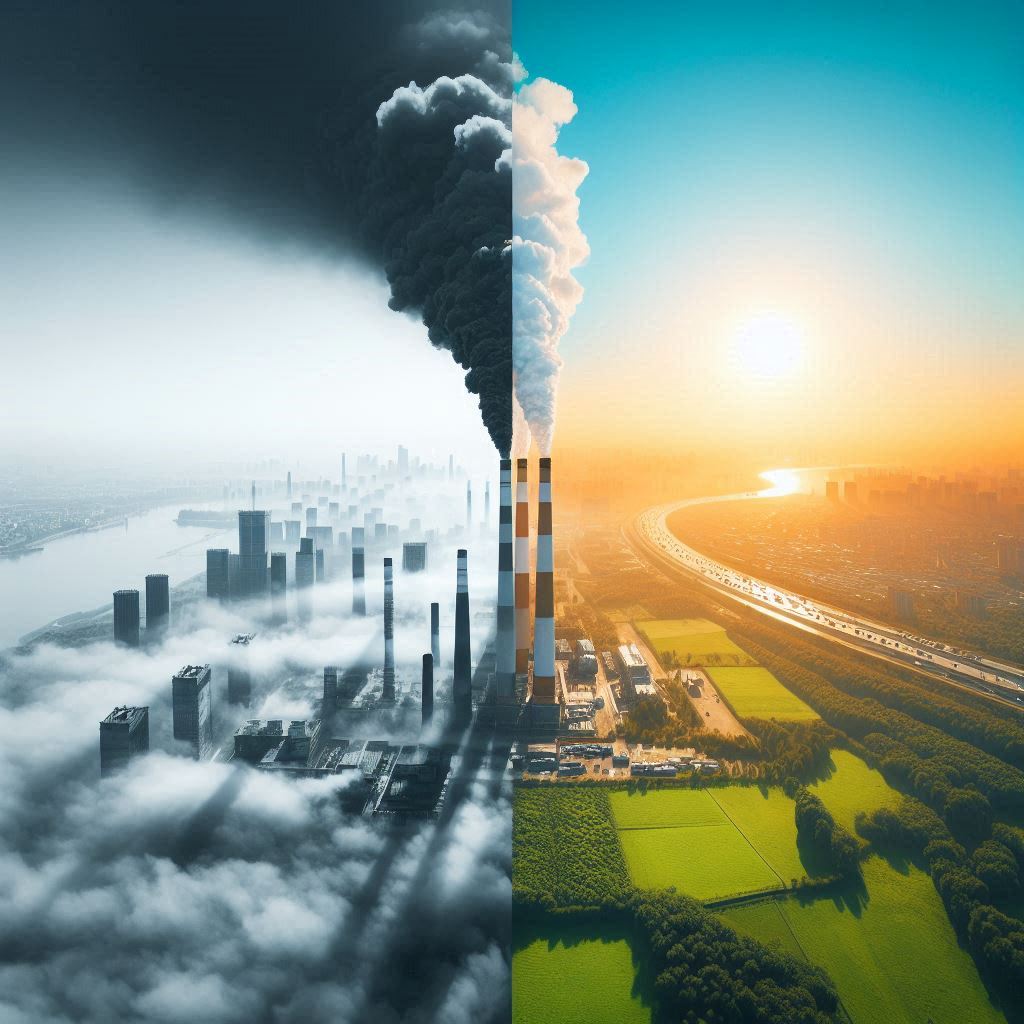
Recirculation, Scrubbing and Filtration Technologies for Controlling Emissions
When emissions reduction at the burner level isn’t enough, recirculation, scrubbing and filtration technologies offer a reliable solution for controlling NOx and SOx. These technologies capture pollutants post-combustion, ensuring that emissions remain within acceptable limits.
Flue Gas Recirculation (FGR)
Flue Gas Recirculation (FGR) is a technique used to reduce nitrogen oxide (NOx) emissions from combustion processes. It works by reintroducing a portion of the flue gases (exhaust gases) back into the combustion air before it enters the burner.
How It Works:
- Lowering Flame Temperature: Since flue gas consists primarily of carbon dioxide (CO₂) and water vapour with little oxygen, recirculating it reduces the amount of available oxygen in the combustion process. This leads to a cooler flame temperature, which in turn limits the thermal NOx formation.
- Diluting Oxygen Levels: With less oxygen in the combustion air, the formation of fuel NOx (which occurs when nitrogen in the fuel reacts with oxygen) is also minimized.
System Setup:
Step 1: A portion of the flue gas is extracted from the exhaust stack.
Step 2: It is then mixed with fresh combustion air before entering the burner.
Step 3: The burner system is specifically designed or adapted to handle the modified combustion process.
The Benefits:
- Significant reduction in NOx emissions (up to 70% in some cases!).
- Can be retrofitted to existing plant.
- Cost-effective compared to some other NOx control methods.
________________________________________________________________________________________________________________________________________
Selective Catalytic Reduction (SCR)
What It Does:
Selective Catalytic Reduction (SCR) is an advanced emission control technology that effectively reduces NOx emissions by converting them into harmless nitrogen (N₂) and water vapour (H₂O) through a catalytic reaction.
How It Works:
Step 1 – Injection of a Reducing Agent: A reagent (typically ammonia or urea is injected into the flue gas stream.
Step 2 – Passing Through a Catalyst: The flue gas then flows through a catalyst bed (usually made of titanium dioxide, vanadium pentoxide, or tungsten oxide).
Step 3 – NOx Reduction Reaction: The catalyst facilitates a reaction between NOx and ammonia to form nitrogen and water vapour, which are naturally present in the atmosphere.
The Benefits:
- Can achieve over 90% NOx reduction, making it one of the most effective solutions.
- Works across a wide range of industrial boilers, power plants, and process heaters.
- Improves regulatory compliance in areas with strict emissions standards.
________________________________________________________________________________________________________________________________________
Electrostatic Precipitators (ESP)
What It Does:
Electrostatic Precipitators (ESPs) are used to remove fine particulate matter (PM) from flue gases, which can include soot, ash, and other pollutants that accompany NOx and SOx emissions. They are widely used in power plants, cement
factories, steel mills, and waste incinerators.
How It Works:
Step 1 – Charging of Particles: Flue gas passes through a high-voltage electric field, which ionizes the particles in the gas stream, giving them a negative charge.
Step 2 – Collection on Electrodes: The negatively charged particles are attracted to positively charged plates (collection electrodes) inside the ESP unit.
Step 3 – Particle Removal: The collected particles form a layer on the plates, which is periodically dislodged using mechanical rapping systems so that the material falls into hoppers for disposal or recycling.
The Benefits:
- Highly efficient (up to 99% removal efficiency) for “fine” to “large” particles and even some heavy metals.
- Reduces emissions that contribute to acid rain, smog, and respiratory illnesses.
- Can handle high-temperature and large-volume gas flows with minimal pressure drop.
________________________________________________________________________________________________________________________________________
Each of these technologies plays a crucial role in reducing air pollution from industrial combustion processes:
FGR is an effective NOx reduction technique that modifies the combustion process to lower flame temperature.
SCR is a high-efficiency solution that chemically converts NOx into harmless components using a catalyst.
ESP is essential for removing fine particulate matter, improving air quality, and reducing environmental impact.
By implementing these technologies, plant owners and operators can achieve regulatory compliance, improve efficiency, and contribute to a cleaner environment.
Strategies to Reduce Operational Costs While Meeting Strict NOx and SOx Regulations
Meeting NOx and SOx regulations doesn’t have to mean increased operational costs. In fact, the right strategies can lead to significant cost savings:
- Optimise Fuel Usage: Advanced burner control systems like SAACKE SCanView and se@vis reduce fuel consumption by improving combustion efficiency.
- Upgrade to Modern Burners: Replacing older burners with low-NOx models can significantly reduce emissions and improve performance.
- Implement Real-Time Monitoring: Digital platforms like ours provide real-time emissions data, helping operators adjust combustion parameters for optimal efficiency.
- Preventive Maintenance: Regular servicing of your burners, and system checks to ensure, scrubbers and filtration systems are operating at peak performance, helps to avoid costly inefficiencies and downtime.
- Energy Recovery Systems: Implementing heat recovery solutions can increase plant efficiency, reducing fuel consumption while maintaining optimal performance. Technologies such as economisers and waste heat recovery boilers can play a significant role in energy savings.
By focusing on efficiency, precision, and modern technologies, businesses can meet strict regulations while reducing fuel costs and improving system reliability – turning compliance into an opportunity for operational improvement.
Achieving Compliance Without Compromise
Navigating NOx and SOx regulations requires a proactive, integrated approach.
As environmental regulations tighten across industries, achieving compliance with NOx and SOx emissions limits requires more than just reactive measures—it demands a forward-thinking strategy. Companies that integrate emission reduction technologies into their operations not only ensure regulatory adherence but also position themselves for long-term sustainability and cost savings.
SAACKE provides a comprehensive suite of solutions designed to help businesses navigate this evolving landscape. From low-emission burners and flue gas recirculation systems to advanced air-fuel ratio controls and real-time emissions monitoring, our technologies enable precise combustion control, minimizing pollutant formation at the source. By optimizing combustion efficiency, our solutions also contribute to lower fuel consumption, reduced maintenance needs, and enhanced overall plant performance.
Beyond technology, SAACKE brings decades of engineering expertise to support businesses in implementing customized strategies for emissions compliance. Our team works closely with clients to assess their unique operational requirements, ensuring that emissions reduction measures are seamlessly integrated without disrupting productivity. Whether retrofitting existing systems or designing new installations, we prioritize efficiency, reliability, and long-term value.
With SAACKE, businesses can meet stringent environmental targets without sacrificing performance. Our proactive, integrated approach ensures that compliance goes hand in hand with operational excellence, future-proofing industries against tightening regulations and rising energy costs.
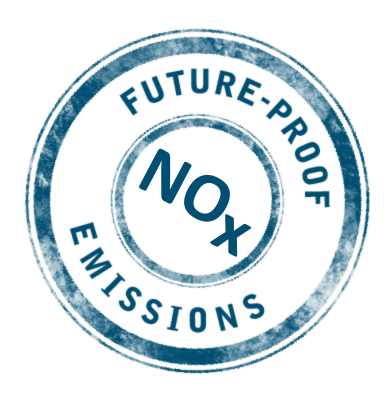
Exciting Times Ahead
The drive for cleaner air and stricter emissions standards is pushing industries to adopt smarter, cleaner combustion solutions. By investing in advanced technologies and implementing robust strategies, businesses can achieve compliance, improve performance, and reduce costs. At SAACKE, we’re committed to helping operators lead this transformation with innovative systems that deliver efficiency, sustainability, and long-term success. As global regulations continue to evolve, staying ahead of compliance requirements will be essential. Businesses that proactively adopt cleaner combustion technologies will not only meet legal obligations but also enhance their reputation as responsible industry leaders.
Want to Know More?
If you are interested to know more about emissions limits, recent regulation enforcements or how you can save money on the running of your plant, Contact our team today and we can arrange a more in-depth presentation for you, or organise an initial free on-site consultation.